
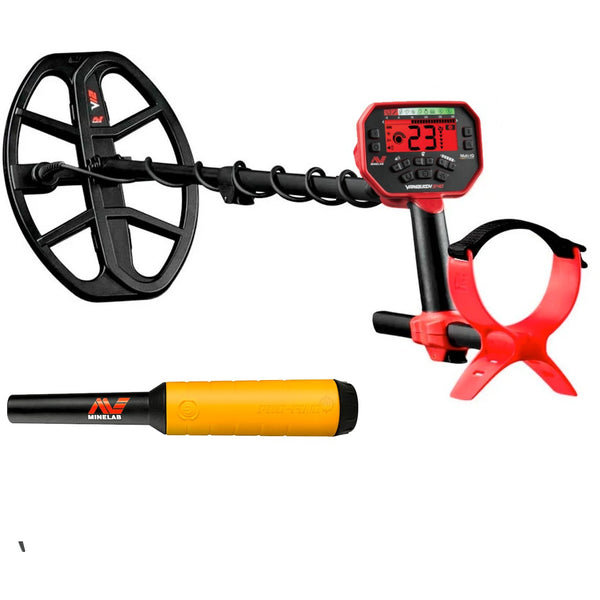
Some devices can be permanently connected to the network and some are handheld for ad hoc use.ĭuring operation, Profibus PA instruments carry a status byte with the process variable in every cycle. Bus and protocol analyzers are available from multiple sources. Profibus PA Troubleshooting DiagnosticsĪfter alarms, which parallel those for Profibus DP, checking the network is a good troubleshooting starting point. Run-time analysis tools perform oscilloscope functions (such as wave forms, signal levels, and reflections) and network topology determinations, and assist in locating cabling errors, faulty devices, etc. Many vendors provide tools for Profibus DP (RS-485).

Alarms can be generated from the process and from the hardware. Profibus DP Troubleshooting Diagnosticsįor Profibus DP, the first line of diagnostics is alarm status. But we will start with Profibus network diagnostics, and then see how Profinet builds upon them. It also adds additional diagnostic capabilities beyond Profibus. Profinet provides a larger address space, faster speeds, and is future-proofed because it leverages Ethernet. New projects use Profinet, but there are still more than 50,000,000 nodes of Profibus installed, with more added every year. Profibus devices have manually adjustable dual in-line package (DIP) or rotary switches Profinet settings are all made electronically. Simply replace the device, and the controller locates and activates it. If a Profibus PA device needs to be replaced and a generic profile is used, set the address and replace the device-even if the device is from a different manufacturer! Profinet offers “Simple Device Replacement,” where a device can be replaced without setting an address or using a configurator or computer. When devices need to be replaced, there are two methods available to speed the task. These protocols can display alarms and conditions in an HMI as well. In addition, for Profinet, standard information technology (IT) protocols can be used to monitor the network. Similar tools are available for Profinet. For a Profibus network, special-purpose tools are available for ad hoc or permanently connected monitoring of the network. The network configuration tools from the controller manufacturer can be used as a first-line diagnostic tool. Furthermore, the protocols notify and convey asset management information that can be used for predictive maintenance or condition-based monitoring.Īnd finally, information about the network itself is available.

In addition, the protocols convey diagnostic information about the variables being communicated: a “flag” accompanying a variable from a process instrument indicates if the value is good or suspect. The protocols themselves define and support the alarms. Control devices (e.g., rack 1, module 3 is missing).Connected hardware (e.g., wire break on digital output 7 ).Process variables (e.g., zone 1 high temperature).The first line of defense is alarms, which can be announced on a human-machine interface (HMI). Profibus and Profinet use multiple means to help prevent and recover from downtime. (A proxy is like a gateway in that it connects and maps two disparate networks, but unlike a gateway, proxies are defined in the Profinet specification.) The proxy concept has been so successful that it has been extended to Interbus, DeviceNet, Foundation Fieldbus, and many others. Profibus integrates into Profinet using a proxy. Profinet runs on IEEE 802.3 wired (and fiber) Ethernet and IEEE 802.11 wireless Ethernet. Profibus PA includes power delivery over the bus and is suitable for hazardous environments. Profibus is one protocol over two different physical layers: RS-485 for Profibus DP in discrete applications and Manchester-encoded, bus-powered (MBP) for Profibus PA in process applications. Both specifications are part of IEC 61158. This diagnostic information can prevent downtime and accelerate Profinet troubleshooting.įirst, an explanation of the technologies: Profibus and Profinet International (PI) created, support, and maintain the Profibus and Profinet standards. One of the strengths of fieldbuses and industrial Ethernet protocols in general, and Profibus and Profinet in particular, is the diagnostic information.
